Hydraulic systems are the lifeblood of countless industrial applications, providing the force and control necessary to power machinery in sectors ranging from construction to manufacturing. Central to these systems are hydraulic directional control valves, specifically the widely used D03 and D05 valves. Understanding these components is crucial for anyone involved in the design, maintenance, or operation of hydraulic equipment. This comprehensive guide delves into the intricacies of D03 and D05 valves, exploring their functions, differences, and applications to help you make informed decisions.
1. What is a Hydraulic Directional Control Valve?
A hydraulic directional control valve is a crucial component in hydraulic systems, responsible for directing the flow of hydraulic fluid to various parts of the system. By controlling the path of the fluid, these valves manage the operation of actuators like cylinders and motors, effectively controlling the movement and force within the machinery.
Key Functions:
- Flow Control: Regulates the flow rate and direction of the hydraulic fluid.
- Pressure Management: Maintains system pressure within desired limits.
- Actuation Control: Determines the movement of hydraulic actuators.
Understanding the operation of hydraulic directional control valves is essential for designing efficient and reliable hydraulic circuits.
2. D03 and D05 Valves: An Overview
D03 and D05 refer to standard mounting patterns and sizes for hydraulic directional control valves, as defined by the National Fluid Power Association (NFPA) and International Organization for Standardization (ISO).
D03 Valves
- Size: NFPA size D03 (NG6).
- Flow Rate: Typically up to 10 GPM (gallons per minute).
- Pressure Rating: Up to 5000 PSI (pounds per square inch).
- Mounting Pattern: Standardized pattern for ease of installation.
D05 Valves
- Size: NFPA size D05 (NG10).
- Flow Rate: Typically up to 20 GPM.
- Pressure Rating: Up to 5000 PSI.
- Mounting Pattern: Larger than D03, suitable for higher flow applications.
3. How Do Solenoid Hydraulic Valves Work?
Solenoid valves are electrically actuated valves using a solenoid coil to control the flow of hydraulic fluid. They are integral to modern hydraulic systems, providing precise control over fluid flow and direction.
Operation:
- Electromagnetic Actuation: An electric current passes through the solenoid coil, generating a magnetic field.
- Spool Movement: The magnetic field moves the spool inside the valve body, changing the flow path.
- Control Signals: Can be integrated with digital control systems for automated operation.
Advantages:
- Precision: Accurate control over fluid flow.
- Automation: Integration with control systems allows for efficient operation.
- Reliability: Durable and capable of handling high pressure.
Image:
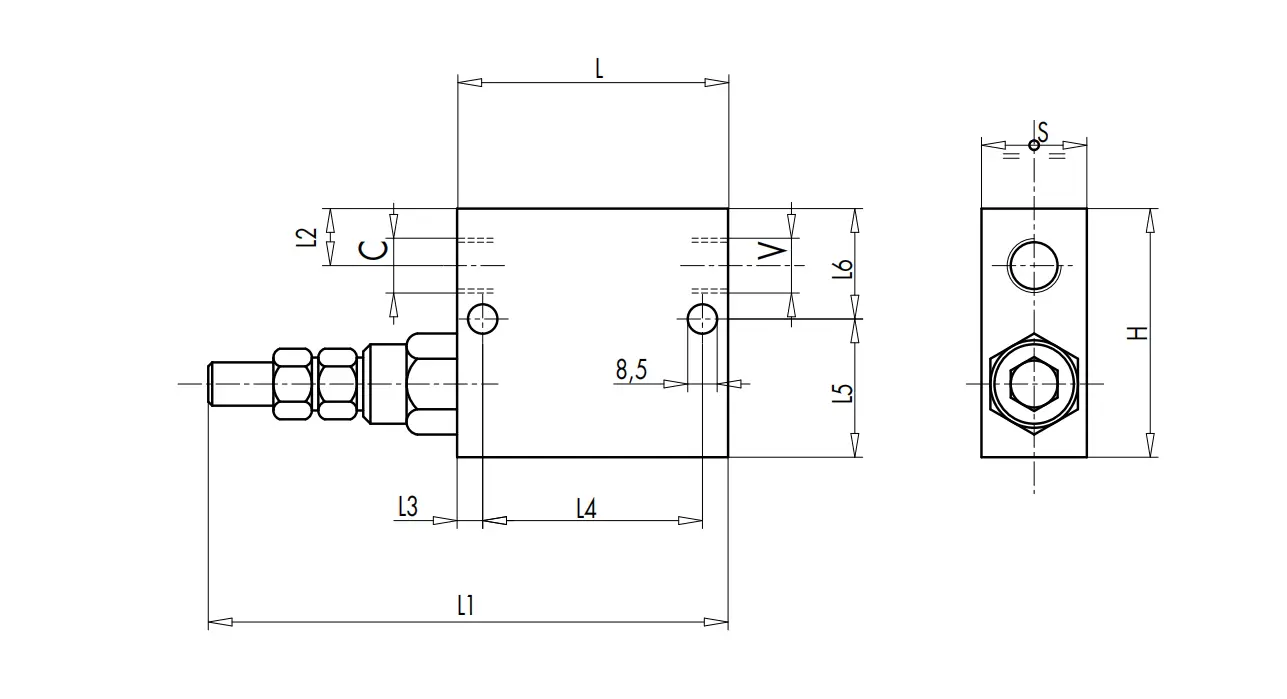
Alt: Direct Acting Sequence Valves
4. Differences Between D03 and D05 Valves
While both D03 and D05 valves serve similar functions, understanding their differences is key to selecting the right valve.
Flow Rate and Size
- Flow Capacity: D03 valves handle lower flow rates (up to 10 GPM) compared to D05 valves (up to 20 GPM).
- Physical Size: D05 valves are physically larger, suitable for systems requiring higher flow rates.
Mounting and Port Size
- Mounting Patterns: D03 and D05 have different mounting dimensions, affecting compatibility with manifolds and subplates.
- Port Sizes: D05 valves have larger ports to accommodate higher flow rates, reducing pressure drop.
Application Suitability
- D03 Valves: Ideal for compact systems with lower flow requirements.
- D05 Valves: Suitable for larger systems where higher flow rates are necessary.
5. Understanding Spool Function and Actuation
The spool is a critical component inside the valve body that directs fluid flow based on its position.
Spool Function
- Directional Control: Determines which ports are connected, controlling actuator movement.
- Flow Paths: Various spool designs (e.g., open center, closed center) offer different flow characteristics.
Actuation Methods
- Solenoid Actuation: Uses electromagnetic force to move the spool.
- Manual Actuation: Lever or hand operation for direct control.
- Pilot Pressure: Uses hydraulic pressure to assist spool movement in pilot operated valves.
Understanding spool function and actuation is essential for tailoring the hydraulic valve to specific system requirements.
6. Direct Operated vs. Pilot Operated Valves
Choosing between direct operated and pilot operated valves depends on system demands.
Direct Operated Valves
- Operation: Spool is moved directly by the actuator (solenoid or manual).
- Response Time: Faster due to direct actuation.
- Flow Capacity: Generally lower flow rates.
Pilot Operated Valves
- Operation: Utilizes fluid pressure (pilot pressure) to move the spool.
- Response Time: Slightly slower due to pilot circuit.
- Flow Capacity: Handles higher flow rates with lower actuation force.
Application Considerations
- Direct Operated: Suitable for systems where quick response and lower flow rates are acceptable.
- Pilot Operated: Ideal for high flow applications requiring reduced actuation effort.
7. Manually Operated Valves: Use Cases
While automation is prevalent, manually operated valves still have their place in hydraulic systems.
When to Use Manually Operated Valves
- Emergency Control: Provides a fail-safe option during power loss.
- Simple Systems: Cost-effective for basic hydraulic circuits.
- Maintenance Operations: Allows manual override during servicing.
Advantages
- Simplicity: Fewer components reduce complexity.
- Reliability: Less susceptible to electrical failures.
- Control: Direct human input allows for nuanced adjustments.
Manually operated valves are essential in situations where human discretion and direct control are paramount.
8. The Importance of Valve Mounting and Size
Proper mounting and consideration of valve size are crucial for optimal system performance.
Mounting Types
- Subplate Mounting: Uses standardized plates (D03, D05), facilitating easy installation and replacement.
- Manifold Mounting: Integrates multiple valves into a single block, reducing space and potential leak points.
Size Considerations
- Flow Requirements: Ensuring the valve's flow capacity matches system needs prevents pressure drop and inefficiency.
- Physical Dimensions: Must fit within the spatial constraints of the equipment.
Image:
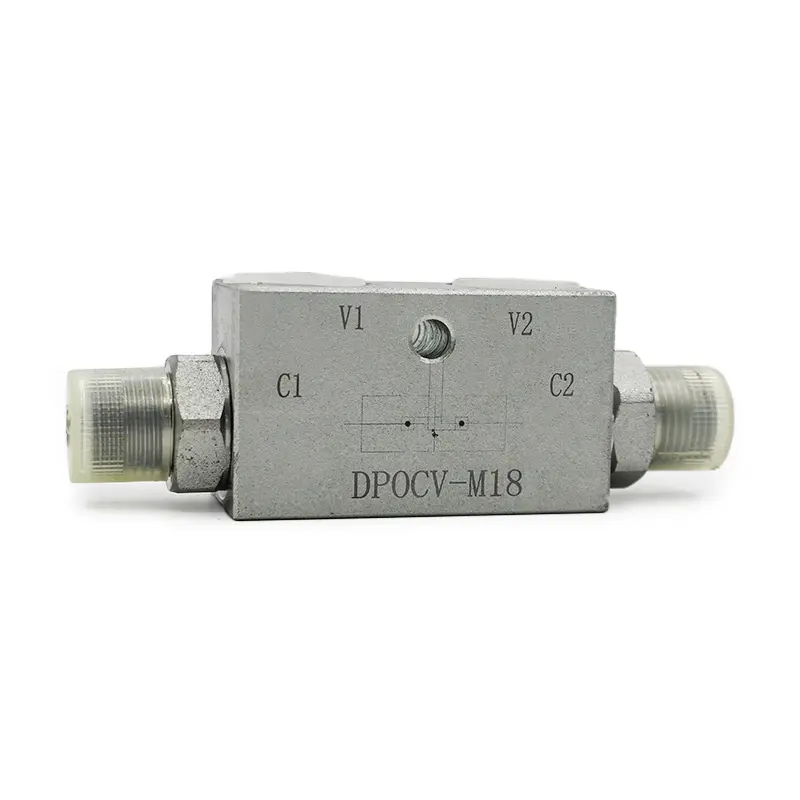
Alt: Double Pilot Operated Check Valves
9. Choosing the Right Hydraulic Valve for Your Application
Selecting the appropriate valve involves evaluating several factors:
Flow and Pressure Requirements
- Flow Rate (GPM): Determine the maximum flow the valve needs to handle.
- Pressure Rating (PSI): Ensure the valve can withstand the system's maximum pressure.
Valve Function and Spool Type
- Spool Configuration: Choose based on desired flow paths and actuator control.
- Operation Method: Decide between solenoid, manual, or pilot operated based on control needs.
Compatibility and Standards
- Mounting Pattern: Verify the valve matches the system's mounting (D03, D05, NFPA, ISO).
- Port Size and Type: Ensure compatibility with existing hydraulic lines.
Consider consulting with experts or suppliers to ensure the valve meets all operational and safety requirements.
Internal Links:
10. Frequently Asked Questions
Q1: How can I tell the difference between a D03 and D05 valve without referencing dimensions?
A1: The main differences are in flow capacity and mounting patterns. D03 valves handle up to 10 GPM, while D05 valves handle up to 20 GPM. Additionally, their mounting patterns are standardized, so identifying the pattern can help distinguish them.
Q2: What does 'direct operated' mean in hydraulic valves?
A2: 'Direct operated' means the spool inside the valve is moved directly by an external force, such as a solenoid or manual lever, without assistance from pilot pressure. This allows for quicker response times.
Q3: Why might I choose a pilot operated valve over a direct operated one?
A3: Pilot operated valves are suitable for higher flow rates and pressures. They require less force to operate the spool, making them ideal for large systems where direct operation would be impractical due to the force required.
Q4: What factors affect the pressure drop across a valve?
A4: Pressure drop is influenced by the flow rate, the size of the valve and its ports, and the internal design of the valve (such as spool type). Selecting a valve with appropriate flow capacity reduces unnecessary pressure losses.
Conclusion
Understanding D03 and D05 hydraulic directional control valves is fundamental for optimizing hydraulic systems. By considering factors like flow rate, pressure requirements, spool function, and mounting size, you can select the right valve to enhance system performance and reliability.
Quick Summary
- Hydraulic directional control valves are essential for directing fluid flow in hydraulic systems.
- D03 and D05 valves differ primarily in size, flow capacity, and mounting patterns.
- Solenoid valves offer precise and automated control, ideal for modern systems.
- The spool function and method of actuation greatly impact valve performance.
- Choosing between direct operated and pilot operated valves depends on system flow and pressure needs.
- Proper mounting and correct size selection are vital for efficient operation.
- Manually operated valves remain important for emergency controls and simple systems.
- Always consider system compatibility, including standards like NFPA and ISO, when selecting a valve.
Further Resources
For expert assistance and a comprehensive range of hydraulic valves, contact our team. We're here to help you find the perfect solution for your hydraulic system needs.
Images Included
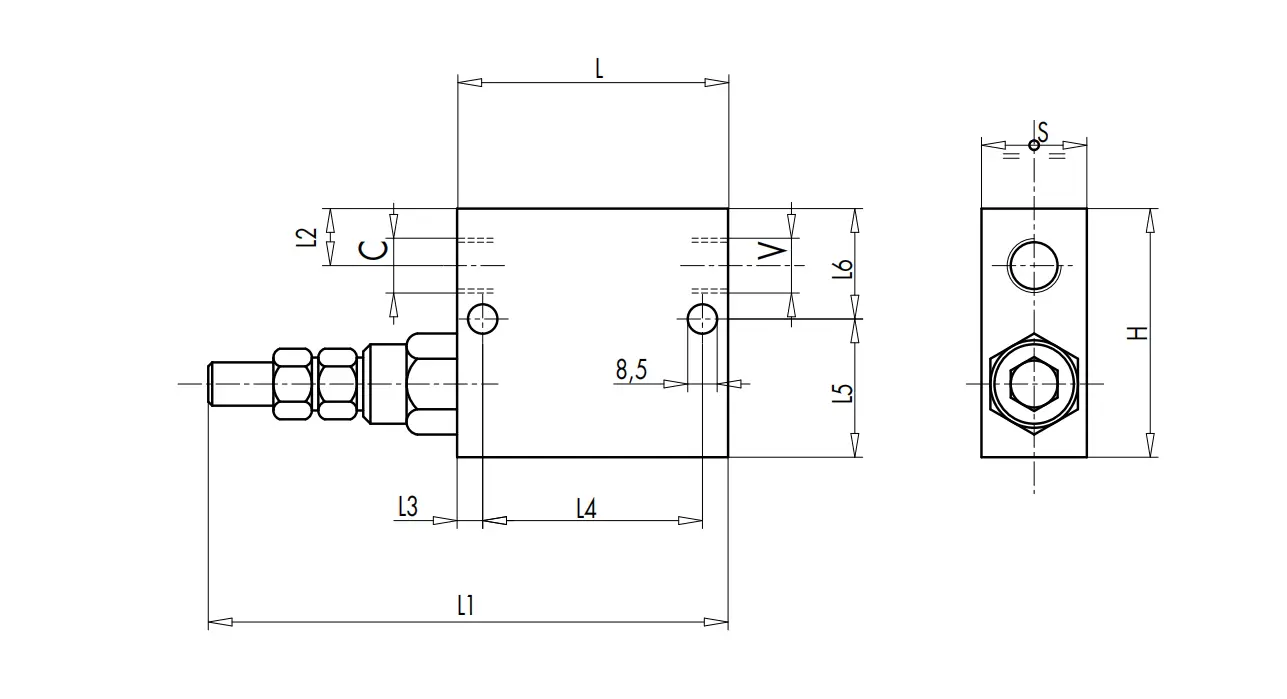
Alt: Direct Acting Sequence Valves
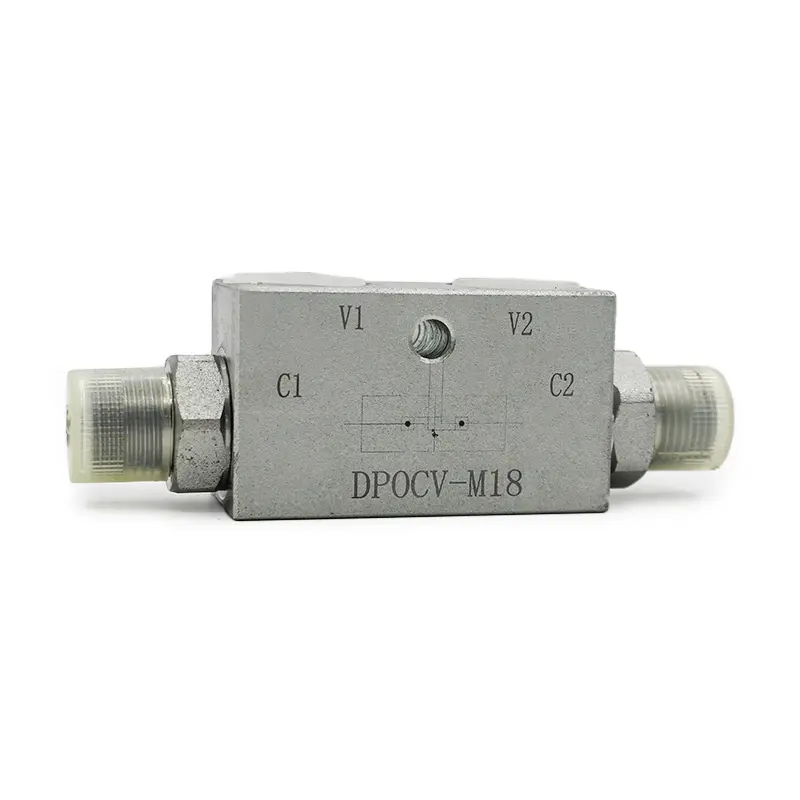
Alt: Double Pilot Operated Check Valves
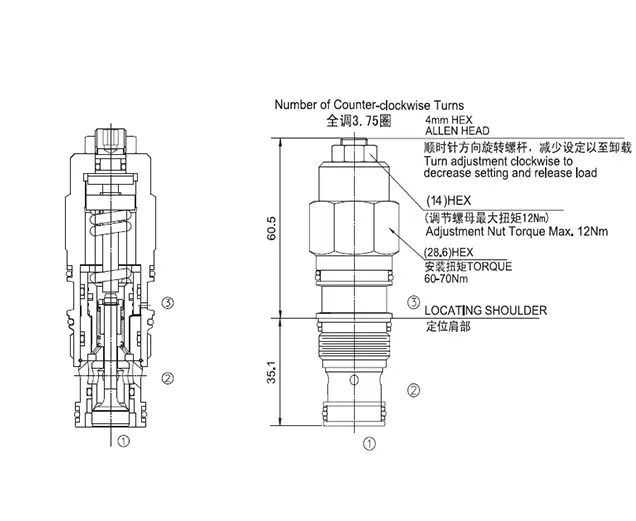
Alt: Relief Valve-Cartridge Type
By understanding the critical role of valves, specifically D03 and D05 hydraulic directional control valves, you can ensure your hydraulic systems are efficient, reliable, and perfectly suited to your industrial needs.